You are having a good day as a quality assurance professional at a small pharmaceutical company until you open an email from your company president asking for an explanation. She is forwarding an email to you from the United States Food and Drug Administration (FDA). The second paragraph in the FDA email reads:
This warning letter summarizes significant violations of Current Good Manufacturing Practice (CGMP) regulations for finished pharmaceuticals. See Title 21 Code of Federal Regulations (CFR), parts 210 and 211 (21CFR parts 210 and 211).
In the red haze that follows, you see the words like “adulterated,” “contaminated,” and “change management.”
The snippet below was taken from a warning letter found on the FDA Warning Letters website , posted 11 May 2023.
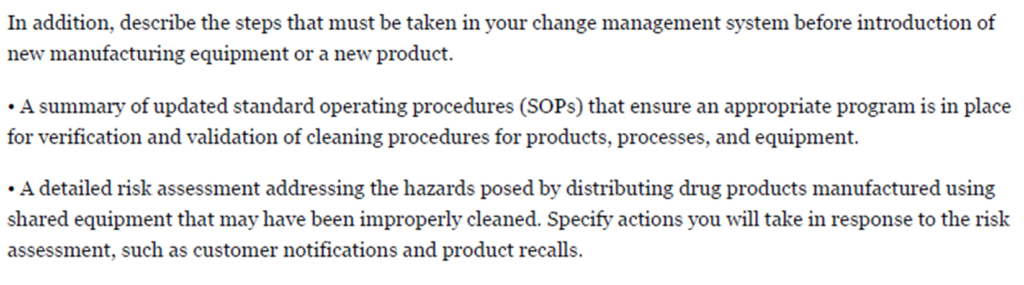
In this blog, we explain best practices for the change management process and associated documentation so that your drug program stays compliant with FDA regulations.
What exactly does “change management” refer to?
The CGMP’s text for small molecule and biologic drugs, located in 21 CFR, part 211.100 subpart (a) states:
“There shall be written procedures for production and process control designed to assure that the drug products have the identity, strength, quality, and purity they purport or are represented to possess. Such procedures shall include all requirements in this subpart. These written procedures, including any changes, shall be drafted, reviewed, and approved by the appropriate organizational units and reviewed and approved by the quality control unit.”
CGMPs for medical devices (21 CFR part 808, 812, and 820) contain similar wording.
Why is change management necessary?
For every drug program, an up and running manufacturing operation has already been commissioned, qualified, validated, and certified to produce satisfactory products in accordance with internal requirements and external CGMP regulations. However, in every manufacturing process, change is inevitable. For example, if
- your production department decides to change the packaging for a finished product;
- the filter that is used to filter your product is no longer available, so you’re changing to a new filter; and
- a new analytical test method is available, so you’re changing to that new analytical test method.
All these potential changes will require change management.
Proposed changes must be assessed to determine their impact on the system. The change management process assures continuous product quality by identifying and addressing the concerns of all responsible groups. It assures a proper evaluation and testing is performed by assessing the continuity of the change across all systems, procedures, and documents for each product and/or dosage(s) everywhere the change is made. This orderly management of changes assures consistent conformance to the identified requirements by assuring critical stakeholder’s input.
Why is change management required?
There are currently no specific requirements for a written change management procedure. However, 21 CFR part 211 suggests that the absence of a written change management procedure is a violation. This violation has appeared on many FDA Form 483 observations (listing FDA audit findings) and resulting warning letters when the items listed on the FDA Form 483 haven’t been sufficiently addressed.
Who needs to be involved in change management?
Depending upon the proposed change, change management may require review by almost any division in the manufacturing company. The change management process typically falls under the quality organization. Other key reviewers are regulatory affairs (to determine the potential of the change to impact a submission), manufacturing, and engineering; but every division in the manufacturing company needs to be considered when assessing the impact of the change.
Ideally, changes should be proposed before changing the drug manufacturing process. A well-defined change plan should be developed and reviewed by the change management committee prior to making the change. This change plan should define the change, including what documentation should be developed to support the change (e.g., validation, regulatory assessment, etc.).
The last step in the change management process is retaining the documentation supporting the change in a change management database. This documentation system should be well-organized and searchable based on the products involved in the change, the change made, the date of the change, the documentation involved, and the regulatory filing status. The change management database should be searchable for changes by product so appropriate documentation is included in annual reports and other filings to the FDA, as appropriate. If the change is submitted as a Changes Being Effected-30 submission or a prior approval submission, include a copy of the approval letter in the change management documentation. Changes that impact global submissions also need to have similar documentation retained.
Takeaways
Briefly, a change management process is a systematic process by which every change to a drug manufacturing process is evaluated by appropriate personnel for impact from a quality, safety, and regulatory standpoint before the change is implemented. Change management identifies all documents and procedures impacted by the change as well as all testing to assess the suitability of the proposed change before implementing it. The change is evaluated by the quality unit and all other relevant functional groups impacted. Finally, the change documentation is retained in an organized fashion such that it may be retrieved, as needed, at a future date.
Do you need help writing the documentation required for change management? Our regulatory professionals can help!